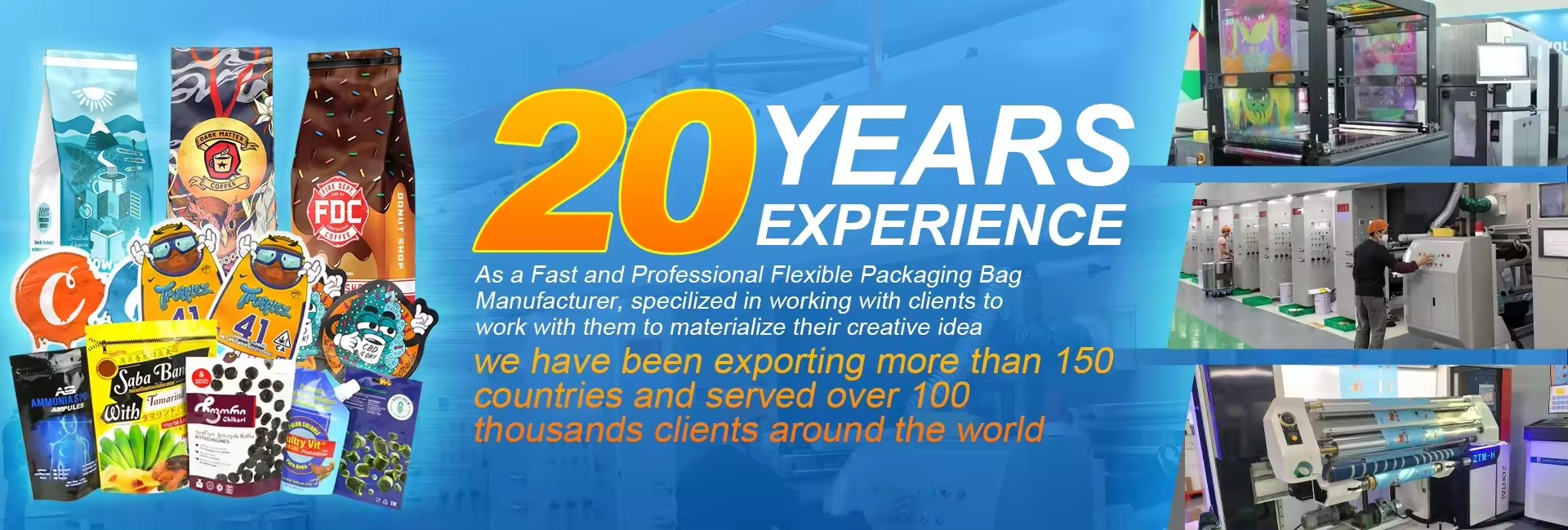
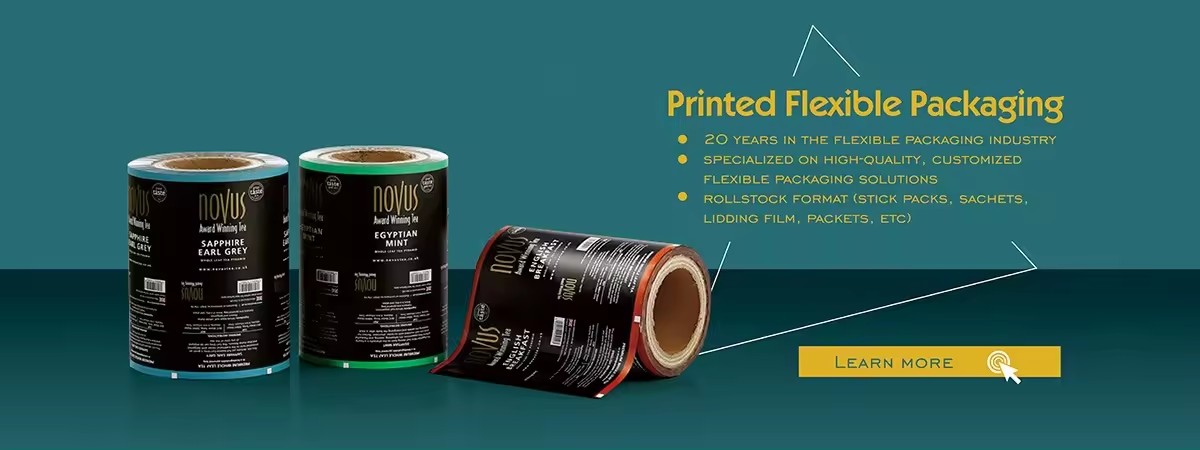
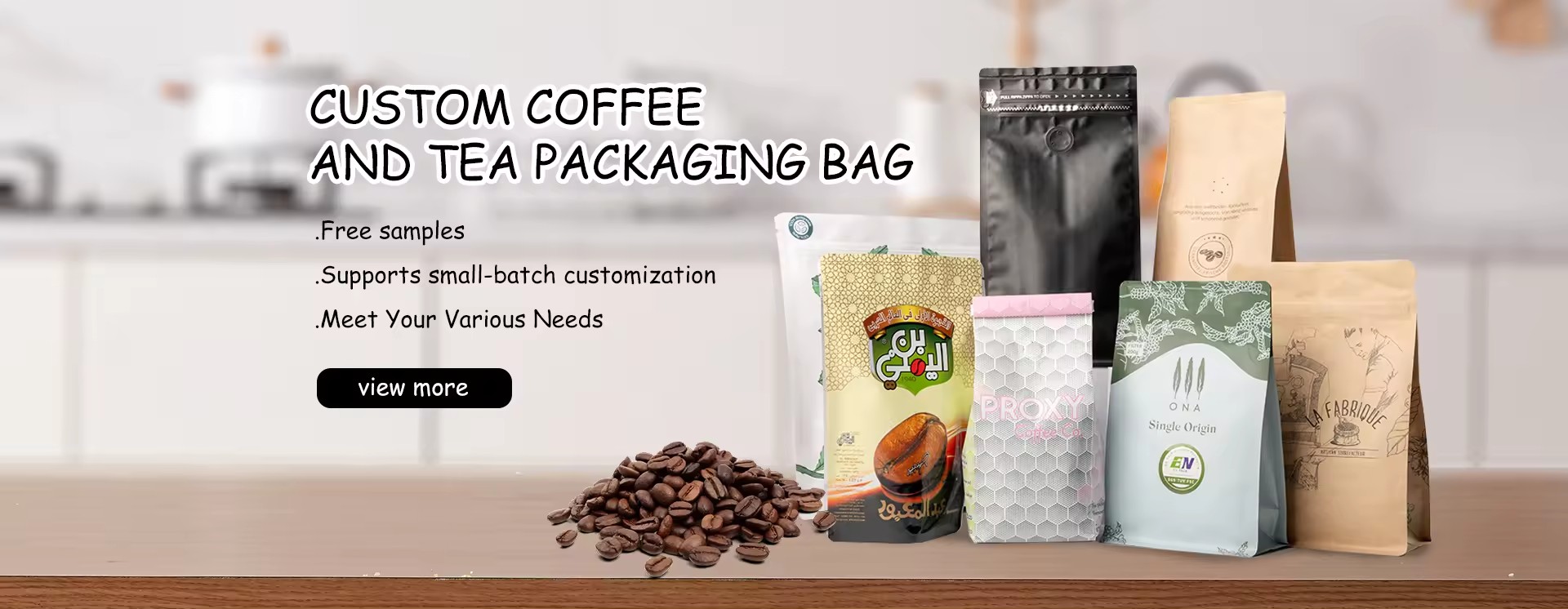
What is an octagonal sealed bag? As the name suggests, it is a new bag type that has emerged in the past two years. The bottom of an octagonal sealed bag is completely different from traditional upright bags, self-supporting bags, or standing bags. The difference is that the bottom of a flat bottomed bag is very flat and does not have any heat sealing edges, displaying text or patterns smoothly; So that product manufacturers or designers have sufficient space to showcase and describe their products, and have good design imagination space, which can perfectly reflect the designer’s design philosophy for product packaging.
Also known as octagonal zippered bags, octagonal upright bags, and square bottom bags, it is a new favorite in the food packaging bag industry. In today’s highly homogenized competition, a unique and technologically advanced packaging bag can increase the product’s gold content, enhance market competitiveness, and facilitate product brand building and promotion.
What is octagonal sealing bag? After that, the production process of octagonal sealing bag from Guangdong Huangpin Yazhi, the manufacturer of octagonal sealing bags, will be introduced:
1. When printing on a film (each color has a plate roller, and the engraving of the plate roller is concave plate engraving), the ink flows continuously during printing because the ink will condense. During ink printing and film printing, a scraper is embedded to scrape off the ink on the protruding areas of the plate roller, so that the concave plate roller can be printed. If there is dust on the scraper, there will be strip like ink contamination. The phenomenon of dot shaped ink pollution is caused by the splashing of ink onto the packaging film during rolling printing, resulting in dot shaped ink pollution.
2. After the film is printed, the composite process begins. For the films produced by our company, the dry wet composite method is generally used, which is to apply glue to the color printed film and then enter a drying process for 2 minutes before compounding with PE.
3. Curing: Cure the film after being glued and compounded. The main effect of curing is to firmly adhere the adhesive, which is usually cured at 50 ℃ for 24 hours. In fact, it is to store the composite film at 50 ℃ for 24 hours. If the time and temperature do not meet the requirements, there will be a phenomenon of loose membrane composite.
4. After curing, the film is then inspected. The inspection involves inputting the printed material of the standard template into the computer, and then passing the cured film through a white screen controlled by the computer. If any unqualified products are found, a black mark will be directly pasted on the film.
5. The film after inspection is cut into sections
6. The cut film is then used for bag making. Bag making is achieved by directly using a machine to automatically seal and compress a piece of film during the bag making process.
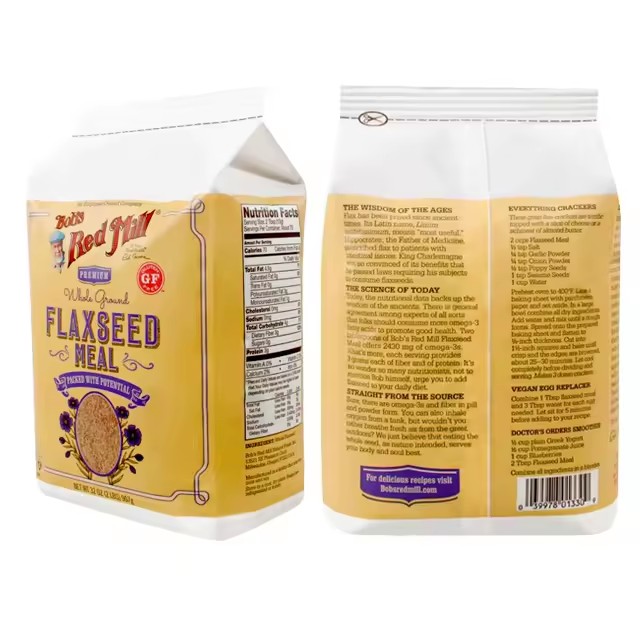
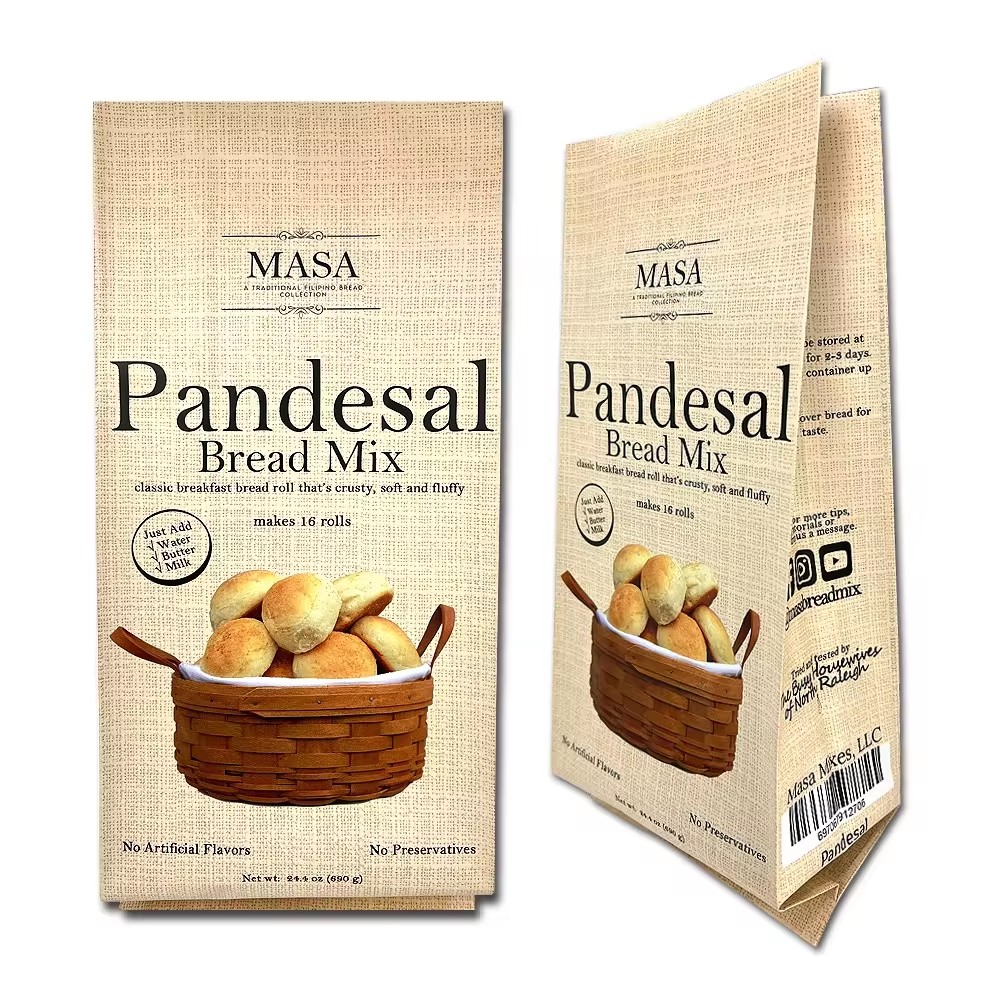